Vertical Storage System - Space Saving Solution
In industry, most of the productive time consumed in material handling and storage, it is necessary to optimize the material handling and storage system. Automated Vertical Storage System (AVSS) is one of the technologies used to store and retrieve the material, tools, and consumable products. This paper summarizes, design of the Automated Vertical Storage System, its adantages and disadvantages.
Automated Vertical Storage System has many benefits, including savings in production time, labour costs, improved material flow, and inventory control, improved throughput, high floor-space utilization, safety for workers, and stock rotation. Trays used to store the materials inside the storage system and delivery the materials without any human resources.
Automated technologies and vertical storage system will save time and optimizes picking operations. It Saves 90% of floor space also, it increases accuracy, product security, and ergonomic functions. It uses warehouse management software associate with the system, which will allow easy control and manage material handling and storage trays with inventory management software and all the information of the materials stored in the software for easy usage at a convenient location.
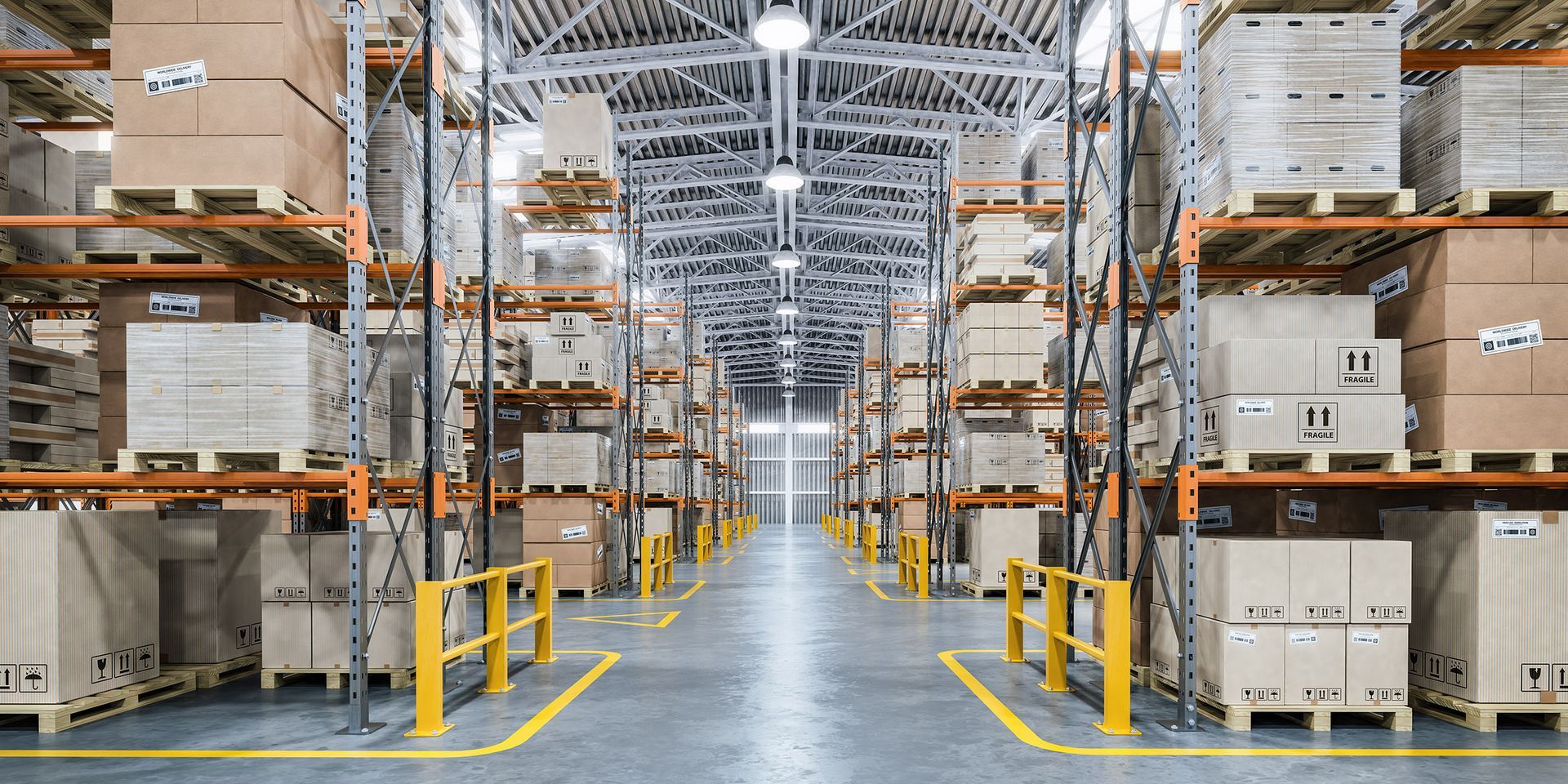
Today’s world of automation, Automatic vertical storage system plays a vital role in handling raw materials, and it is challenging to handling materials and storage consumption in large industries. (AVSS) the system used to handle space constraints; also, it reduces the flat surface space in industries and material handling. In this paper, the design of, Automatic vertical storage system (AVSS) discussed, the system increases the utilization of vertical air space and decreases the flat surface space consumption.
In the olden days, the way of material handling done using animals and carts, but know the technology developed with the advancement of science by using forklifts and conveyor belts. The first (AVSS) introduced in 1940 Automatic vertical storage system with Automated guided vehicle introduced in 1950; it reduces the maximum time for manual retrieval. Automatic Vertical Storage System is a vital part of the model logistic system, with the consideration of limited space quantity, management control, flexibility, and reliability. The first implemented step for automation in material handling was Automatic guided vehicle is in use after 1950. The Carousels storage system also widely used for picking small, less weight, and commonly used materials. At the stage first, much-improved efficiency and solidity system was AVSS. Storage handling is a vital function in the automation system. Automated vertical storage systems generally used in industries, warehouses, and the primary function which is involved in this system.
It can perform without human action, interference, and supervision. Due to more reliability, it can also reduce the error which is happening while functioning. One major disadvantage was that material should be handled manually before automation, but the automated operation can increase efficiency. This system contains certain features in common, which regarded as cranes, bins, and racks. Before the development of the physical layout of the storage system must be designed; because of the relative flexibility, it tends to occur an error.
Generally, Automatic vertical storage systems used with both the standard and non-standard loads, which means that every standard load must be fit in uniformly sized. This system contains a different variety of software controlling for automated handling and retrieving of materials from a specified storage location. The automatic vertical storage system consists of ninety racks with it, which reduces the space in an industry which can be used for installing the other purposes like installing more instruments to perform manufacturing operations, it is easy to identify and get the latest part which has to perform first. One major thing is that it reduces the time to get parts from the machine while in manual we have to search for it also increases the time to receive certain materials parts.
OBJECTIVES OF THE VERTICAL STORAGE SYSTEM
One of the main objectives is to eliminate warehouse management problems. i.e., lack of flat surface in the industry, inventory problems, material handling, and storage. The primary aim to design an automated vertical storage system in a particular way so that it can store and pick up the materials. Some other objectives are :
1. To increase factory flat surface presently used for storage work-in-process and also to increase the storage capacity.
2. To optimize security
3. To store the materials free from the rust.
4. To optimize safety in the storage function.
5. To reduce labor costs and increase labor productivity in storage operations.
6. To improve inventory control management of the system.
7. To improve storage densityacity.
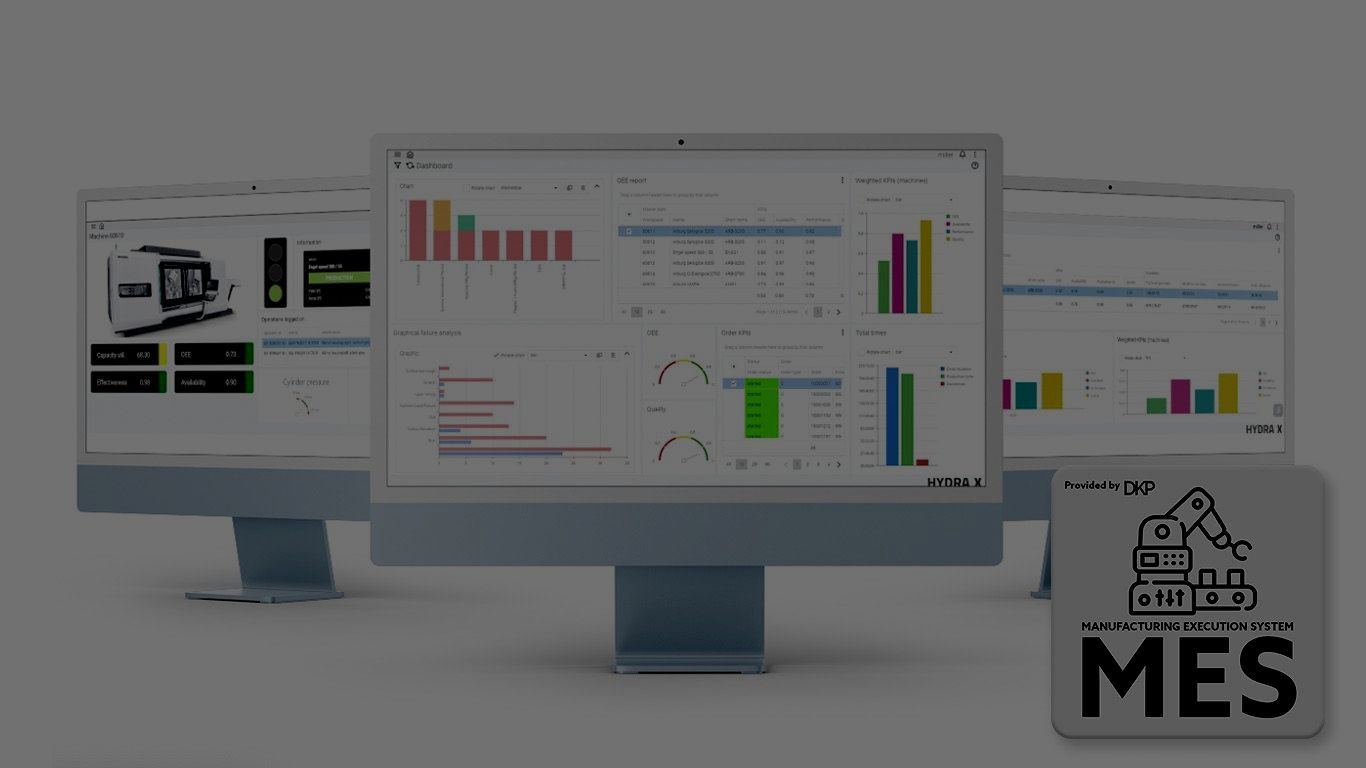
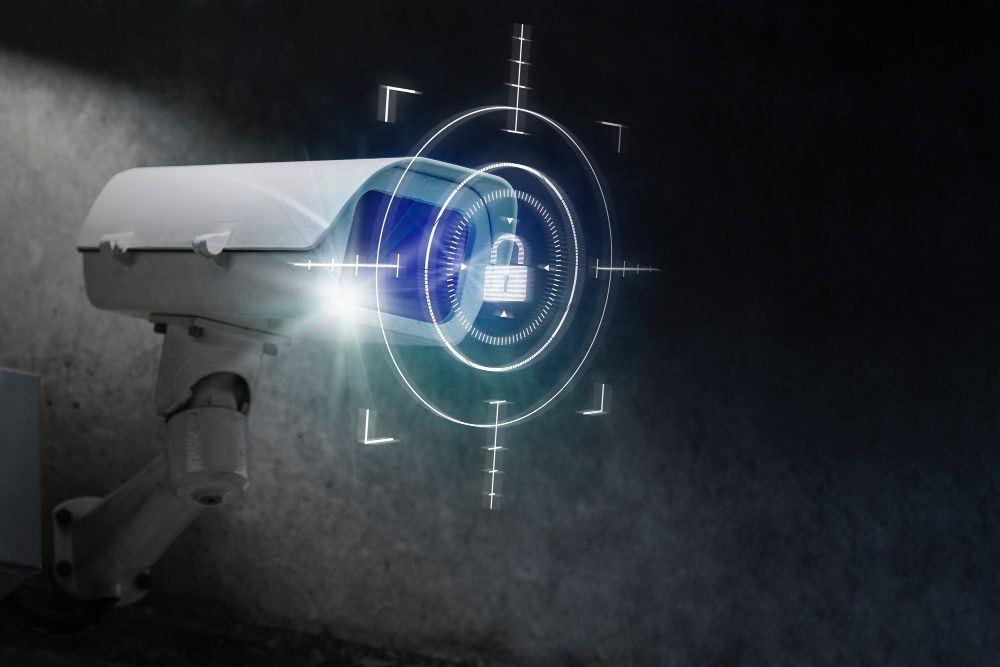